Knurling is a manufacturing technique typically performed on a lathe that involves creating intricate patterns on the surface of a part. These patterns can consist of straight lines, angles or interlocking designs. The knurling process improves the durability and aesthetics of a part while increasing its grip. However, you should know that knurling patterns can be varied. It can have straight ridges or a spiral arrangement of these “straight” ridges, as opposed to the more traditional criss-cross design.
Knurling is an effective way to refurbish parts. This is because the raised portion of the knurled surface helps to minimize the effects of wear and tear on the part. It also plays a role in assembling metal pins into plastic molds.
Knurling is used in the production of a wide range of products such as tool handles, automatic pencils, pistol grips, barbell rods, and more. In addition, knurling is commonly used in dart grips and pedals for BMX bikes. It is also commonly used in the production of surgical instruments.
Table of Contents
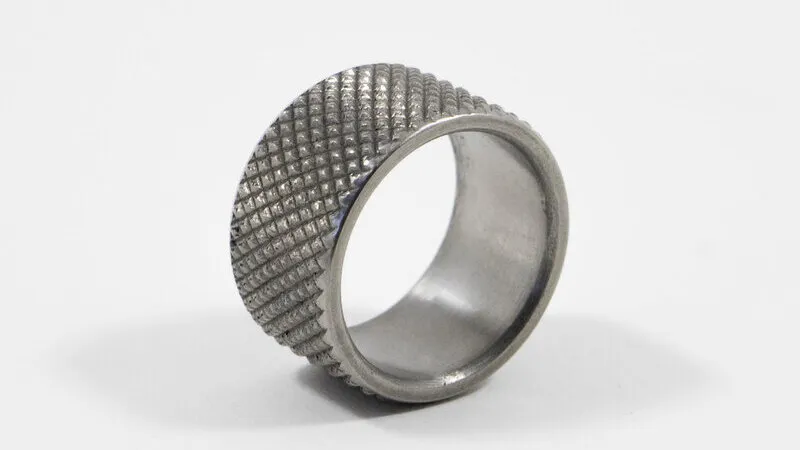
1. Hand Knurling and Machine Knurling
There are two types of knurling techniques: hand knurling and machine knurling. Let’s take a look at each process:
01 Hand knurling
Hand knurling requires the use of a manual knurling tool called a hand knurler. Depending on the setup, this tool may contain one or more knurling wheels. The knurling wheels are usually in the form of compact rolling devices whose surfaces are decorated with patterns such as diamonds or diagonal lines.
When a manual knurler is firmly seated on the surface of a material and begins to run, the rollers exert pressure on it. This causes the material surface to deform and change. However, manual knurling is fundamentally inaccurate, and its operation must be continuous and uninterrupted to prevent overlapping knurling lines.
This process is typically used for small workpieces that can be handled and manipulated manually. As a result, it produces simple knurling patterns, whereas the manual process is useful for complex machining.
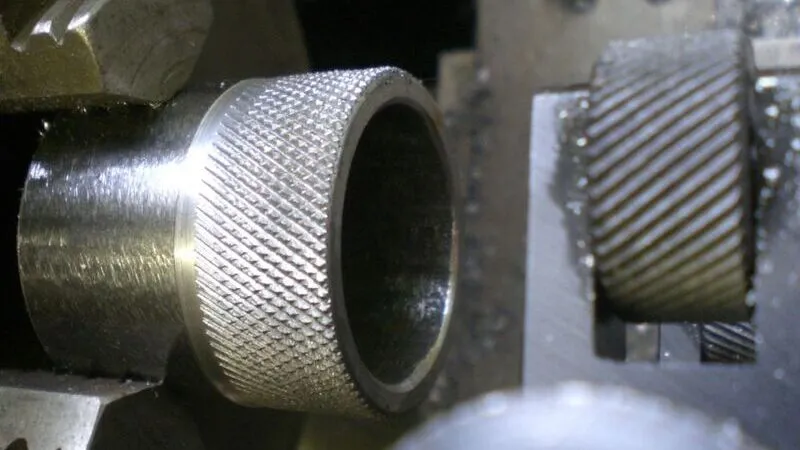
02 Machine Knurling
The machine knurling technique is executed using a machine, usually a manual or CNC lathe. First, the workpiece is securely fastened to the lathe. Subsequently, a wheel is secured to a knurling support and fastened to the table. The machine knurling process involves the wheels touching the workpiece to create the desired knurling pattern. This knurling operation is performed continuously and is usually error-free.
To ensure smooth operation and ease of cutting, the blank is usually lubricated prior to turning. This prevents overheating and enhances the interaction between the blank and the cutting tool. In addition, constant chip removal must be maintained to prevent buildup, which can lead to machine interruptions and defects.
Machine knurling accommodates workpieces of all sizes, lengths and materials. Complex knurling patterns with fine spacing can be produced using precision tools and feeds, ensuring tight control of dimensional accuracy.
2. Knurling Process
The knurling technique involves the use of specialized knurling wheels to produce the desired pattern on the surface of the workpiece. The following describes how the process is executed:
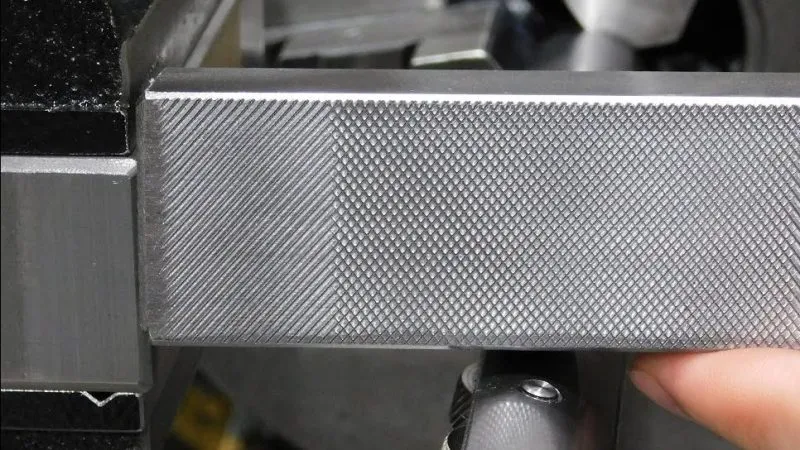
Step 1: Selecting the Right Workpiece Material
When pressing with a knurling tool, the material must be ductile enough to move. Aluminum, brass, mild steel and various plastics are common materials to work with. Harder materials may require the use of special knurling tools and lower speeds.
Step 2: Choose the right knurling method
Hand knurling and machine knurling are the two most common knurling methods. The former uses a small roller tool to press onto the surface of the workpiece to create the desired pattern. The latter uses a lathe to cut the desired pattern into the workpiece. Hand knurling is best suited for softer metals, but machine knurling allows for finer detail in harder materials.
Step 3: Setting up the knurling wheel or tool
Knurling wheels come in a variety of tooth shapes, angles and materials for a variety of uses. The tooth shape determines the pattern and strength of the knurling. They are held in place by a knurling bracket mounted on the workbench. The knurling tool contains a reverse picture of the expected knurling pattern.
Step 4: Mounting the Workpiece Correctly
The workpiece is secured between centers or in a lathe chuck. The workpiece must be correctly clamped to prevent the workpiece from sliding under the knurling stress.
Step 5: Execution of the knurling operation
The rotating workpiece is gently fed by the knurling wheel or tool. Vertical alignment and constant pressure are essential in order to obtain a uniform knurling effect. The surface of the material is then deformed as the wheel or tool is continuously fed into the workpiece while applying constant pressure. This results in bumps or depressions on the surface of the workpiece. In harder materials, sharp, high knurling may require multiple passes.
3. Knurling Pattern Types Explained
01 Straight/standard knurling
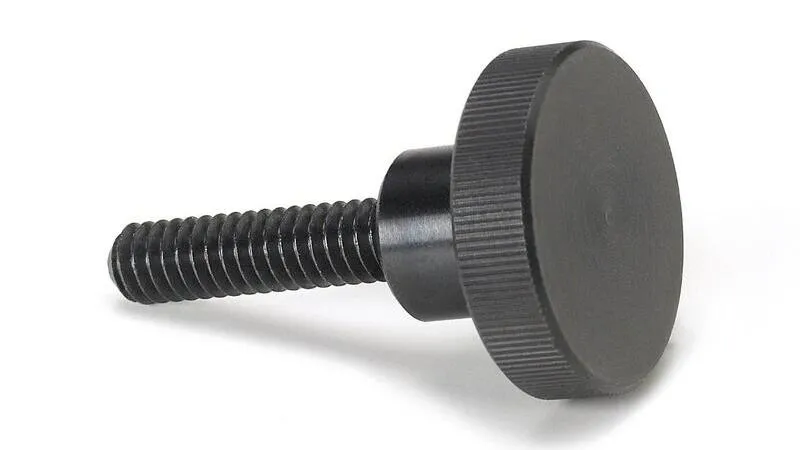
Straight knurling wheels allow the engraving of straight lines and groove patterns on the surface of a workpiece. The technique usually involves creating intersecting lines (either parallel or diagonal) by means of a specialized knurling tool equipped with two hardened wheels with diagonal teeth.
Straight line knurling pattern designs can be used as decorative patterns to enhance the visual appeal of various workpiece surfaces. This technique is ideal for use on cylindrical objects such as handles and knobs. In addition, it proves to be a suitable choice for a variety of uses, including luxury writing instruments, custom hardware or jewelry, giving it an elegant and stylish look.
02 Knurled diagonally
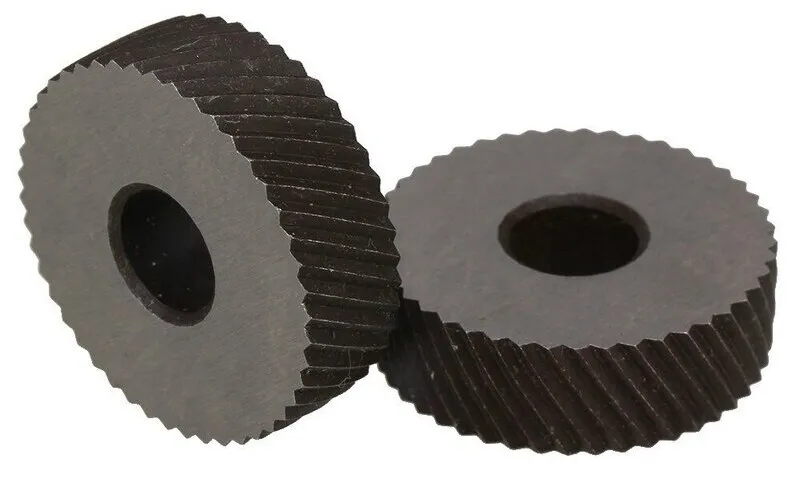
Diagonal knurling is a specialized process used in a wide variety of industries to impart a textured design or gripping properties to cylindrical or round surfaces. It is divided into two categories:
Left-handed diagonal knurling
When viewed from the end of cylindrical objects, they exhibit a diagonal ridge that slopes from the upper right to the lower left. Knurling tools configured with ridges that match this pattern are used to create left-hand knurling. These particular knurls perform their function when rotated counterclockwise or turned to represent the preferred direction.
Right-hand diagonal knurling
When viewed from the end of cylindrical objects, they exhibit diagonal ridges that slope from the upper left corner to the lower right corner. These knurls are formed using a knurling tool with ridges that fit in this direction. Right-handed knurling is usually used when there is a clockwise rotation or turning motion.
03 Knurled diamond
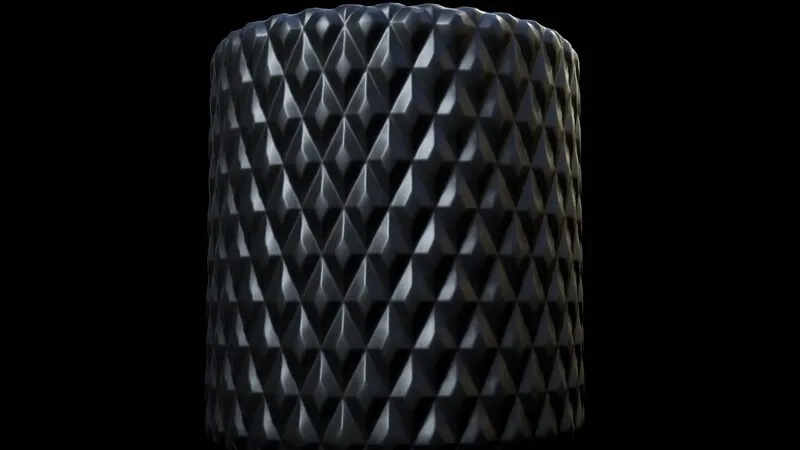
Diamond knurling is a standard method of creating a pattern of small diamond-shaped convex ridges or indentations on the surface of a workpiece. It involves a combination of cross-diagonal lines that form multiple diamond-shaped bumps. Individual diamond knurling wheels enhance the wear resistance and overall durability of the workpiece and are widely used on machine parts, tools, and decorative items that are subject to frequent contact or high friction.
The diamond-shaped indentations or textures evenly distribute pressure and wear, reducing the risk of damage or breakage. The technology produces intricate and aesthetically pleasing knurling patterns on machined parts such as bicycle parts, lighter housings or personal accessories.
04 Special knurling
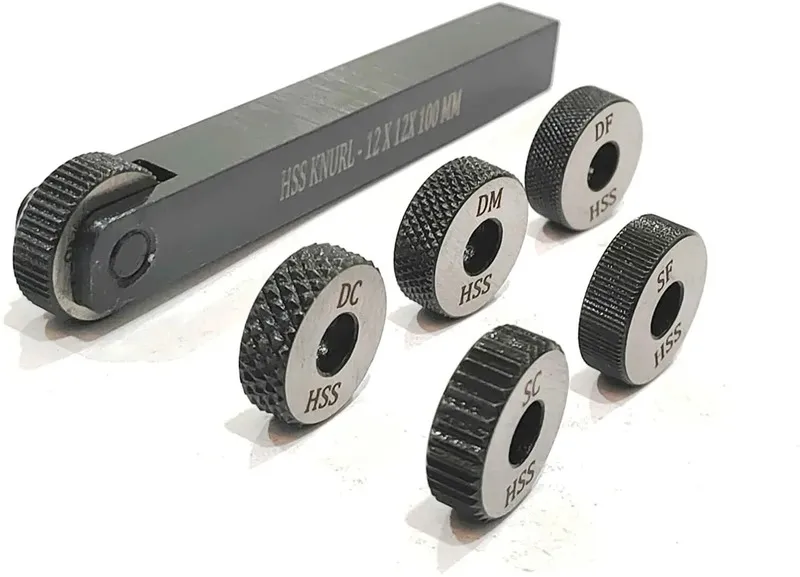
For concave knurling, the teeth on the knurled wheel have a curvature towards the center of the wheel surface. This configuration is typically used to engage and manipulate a single portion of the workpiece in an axial direction.
In contrast, convex knurling is best suited for long transverse knurling operations. Its rounded shape facilitates smoother movement across the surface of the workpiece.
Beveled knurling is another variant, consisting of inclined or sloping ridges that form a distinctly beveled edge on the workpiece. These special types of knurling are often used for aesthetic or practical purposes.
4. Practical Benefits of Knurling
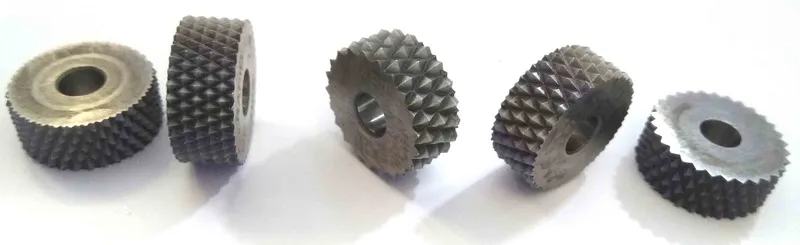
01 Enhanced Grip and Safety
Knurled surfaces increase surface friction to maintain a firm grip even in slippery conditions. This improves safety and control. Knurling on components such as bolts, knobs, wheels and rollers helps prevent slippage during assembly or use.
02 Aesthetic Enhancement
In addition to its practical benefits, knurling adds aesthetic appeal to items. Knurling creates textured patterns that are visually appealing and exciting to look at.
03 Improved Paint Adhesion and Brand Recognition
Knurling increases the surface area of the material, which benefits brand identity and paint adhesion. A textured surface improves paint adhesion for a longer-lasting effect. Manufacturers can also use knurling patterns to add brand identity elements to their products.
04 Functional Availability in Various Industries
The knurling process benefits a wide range of industries. From plumbing fixtures to automotive parts, knurling is used in a wide range of engineering and manufacturing applications.
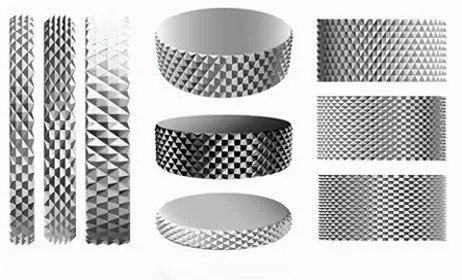
5. Challenges and Limitations of Knurling
01 Material Considerations
Not all materials are suitable for knurling. The hardness and flexibility of the material must be considered when choosing whether or not to use knurling. Some materials, including soft plastics, may not be able to withstand the process and may be deformed or damaged.
02 Surface Finish and Accuracy Requirements
Accurately knurling with proper surface finish can be challenging. The technique may leave burrs or other imperfections. Additional machining or surface preparation is required to meet quality standards. Some procedures are needed.
03 Potential Weakening of Surfaces
Knurling can sometimes weaken materials, especially if it has a complex design or is used on fragile materials. Engineers and manufacturers must carefully weigh the pros and cons of enhanced grip against potential structural defects when employing knurling.