1. Hard Anodizing
Hard Anodizing is a special electrochemical film forming process in aluminum alloy anodizing, aiming at obtaining a thicker, harder, more wear-resistant, less porous and higher breakdown voltage-resistant oxide film than the ordinary anodic oxide film. It is widely used in industrial parts (such as aerospace, hydraulic systems, transmission parts, wear-resistant workpieces, optical instrument bases, and parts of the cookware) that require high wear resistance, high insulation, good corrosion resistance or specific thermal properties.
2. Process Characteristics of Hard Anodizing
① The tank temperature of hard oxidizing is very low, it is recommended to be around 0℃, which requires a powerful freezer and a stirring circulation device. The lower the temperature, the better the quality of the oxide film.
② The sulfuric acid concentration of hard oxidation is low, it is recommended to be around 130g/L, and the aluminum ion content is controlled in the range of 5~10g/L, which is better.
③ The current density of hard oxidizing is higher, and the voltage is larger. It is recommended that the voltage is more than 30V and the current density is more than 2.5A/dm2, and the specific electric parameters need to be determined together with the tank temperature, sulfuric acid concentration and alloy material.
④ Pulse power supply or special waveform power supply is used, and the step-up phase adopts the way of gradual incremental pressurization, which can avoid the material burning under too high voltage on the one hand, and promote the growth of oxidized film in accordance with the normal way on the other hand.
⑤ Hard oxidation can also add some organic acids to the tank solution. Organic acid can improve the hardness and toughness of the oxide film, but also directly using organic acid solution to perform the oxidation process, for some special occasions, parts oxidation.
⑥ Oxidation time: according to the target film thickness to determine, generally in 60-120 minutes or longer.
⑦ Strong stirring: must ensure that the strong circulation of the tank liquid stirring, in order to take away the reaction heat, to maintain a uniform tank temperature, to prevent the workpiece localized overheating.
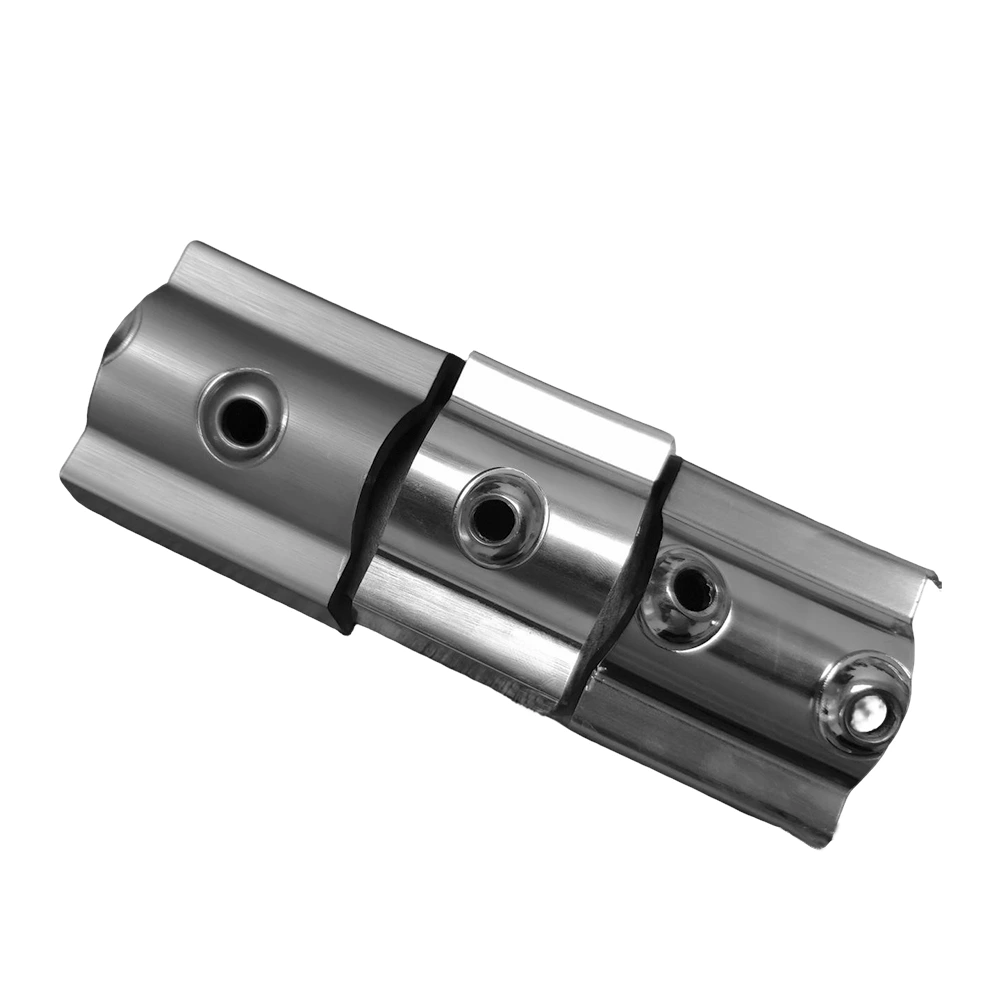
3. Difference Between Hard Anodizing and Ordinary Anodizing
1. Thickness is different:
Hard oxidation is thicker than ordinary oxidizing, generally ordinary oxidizing film thickness of 8-12 μm, the hard oxidizing film thickness is 40-70UM μm.
2. Hardness is different:
Hardness: ordinary oxidizing is generally HV250–350, hard oxidizing is generally HV350-550.
3. Temperature is different:
Ordinary 18-22 ℃, with additives can be up to 30 ℃, the temperature is too high, easy to powder or crack, hard oxidation is generally below 5 ℃, relatively speaking, the lower the temperature, the higher the hardness. The temperature is different: ordinary 18-22℃, additives can be up to 30℃, the temperature is too high, easy to appear powder or cracks, hard oxidation is generally below 5℃, relatively speaking, the lower the temperature, the higher the hardness.
4. Good abrasion resistance: thanks to the higher hardness and lower porosity, the abrasion resistance of hard oxide film is usually 1-2 times higher than that of ordinary oxide film (except for 2 series aluminum alloy).
5. Low porosity & high breakdown voltage: The denser structure and low porosity of the film make it an excellent electrical insulator, with breakdown voltages up to 1000V or more. Increasing the oxidation voltage can further increase the breakdown voltage.
6. Higher corrosion resistance: The dense film layer provides better basic corrosion resistance. However, the effect of microcracks should be noted, and post-processing (e.g., sealing) is critical to the final corrosion resistance.
7. Good thermal emissivity: Hard oxide films are good heat emitters (“blackbody”), their thermal emissivity increases significantly with film thickness, facilitating heat dissipation, and they are used in some applications where heated parts (e.g., some cookware) need to be eliminated from hot spots.
8. Appearance and Surface Flatness:
o Typically an opaque light to dark gray, with depth of color dependent on alloy composition and film thickness. The surface is rougher than normal oxide films.
o The surface is rougher than ordinary oxide film, and as the film thickness increases, microcracks are likely to appear, and the surface flatness is slightly poorer.
o For example, ordinary 6 series alloy hard oxidation often shows a gray-yellow appearance, and is accompanied by micro-cracks.
9. Impact on the mechanical properties of the substrate: The hard oxidation process itself generally does not affect the strength of the material, but may reduce the ductility and fatigue strength of the material, and this effect increases with the increase in film thickness.
10. The essence of the process: Although hard oxidation in the film performance significantly improved, its basic film-forming principle and ordinary anodic oxidation are not essentially different, the core lies in the more stringent control of process parameters to achieve a qualitative change in the performance of the film.
4. Characteristics of Hard Anodizing of Different Aluminum Alloy Series
① 1 Series pure aluminum alloys (e.g., 1050, 1060, 1100) it is the easiest to anodize, hard and get high insulating and high hardness oxide film.
② 2 series aluminum-copper alloy (e.g., 2014, 2024, 2A12), hard anodizing is more difficult. Mainly contains copper-rich intermetallic compounds, preferentially dissolved in the oxidation process, resulting in discontinuous oxide film or pinhole defects. The solution is generally the use of AC and DC superimposed or pulsed power supply, changing the composition of the electrolyte and electrical parameters to avoid the 2 series alloys of hard oxygen defects.
③ 3 Series Aluminum-Manganese alloys (e.g., 3003):
o Difficulty: Medium.
o Characteristics of the film layer: film-forming properties and film quality between the 5 series and 6 series.
④ 5 series aluminum-magnesium alloy (e.g., 5052, 5083, 5A06), the technical difficulty of hard oxidation is general, the hardness of the film layer is slightly worse than that of the 6 series alloy, and there are problems such as burns and excessive film thickness.
⑤ 6 series aluminum-magnesium-silicon alloy (such as 6061, 6063, 6082), hard oxidation difficulty is general, belongs to the alloy is relatively easy to get a high-quality oxidation layer, which plays a relatively large role in the film quality. Copper, iron generally cause the reaction of the components.
⑥ 7 series aluminum-zinc alloys (e.g., 7075, 7A04), hard oxidation is more difficult, there are oxidation defects such as pinholes, and the hardness and wear resistance of the film layer are slightly worse than that of 6-series alloys.
Generally, from the point of view of film formation efficiency and oxide film quality of hard oxidation, the order from excellent to poor is:
1 series → 5 series → 3 series → 6 series → 7 series → 2 series
5. Sulfuric Acid Solution Hard Oxidation Process and Parameters
Free sulfuric acid concentration: 100~150g/L
Aluminum ion content: 1~5g/L
Oxidation tank temperature: (0±2)℃
Current density: (3.5±0.5)A/dm2
Oxidation time: 60~120min
Tank agitation: strong circulation agitation of the tank
Anodic oxidation film thickness: 50~100μm
Closed hole treatment: Generally may not be. However, when sealing is required, it is not recommended to use medium-temperature, medium-high-temperature, high-temperature nickel (without nickel) sealing or pure water boiling water sealing. It is recommended to use normal temperature with nickel or normal temperature without nickel sealing, which not only enhances the corrosion resistance of the oxide film, but also does not lead to a decrease in the abrasion resistance of the oxide film.
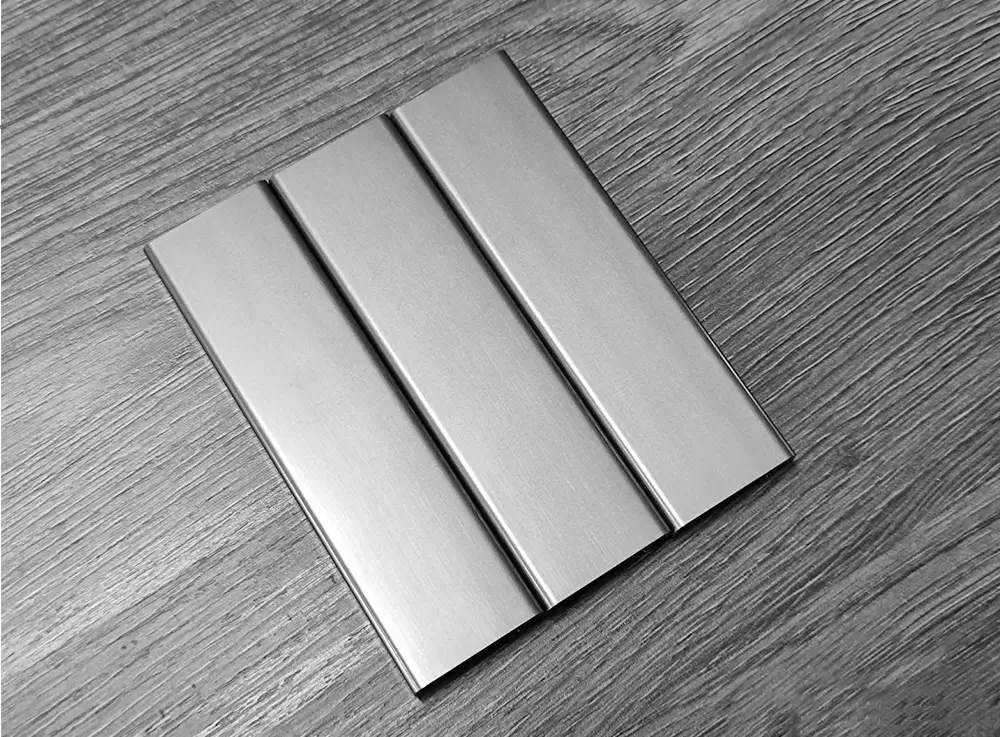
6. Overview of the Performance of Hard Anodic Oxide Film
① Appearance and color
Usually, the hard oxide film is relatively rough, there are micro-cracks, and the film color is closely related to the type of aluminum alloy and the thickness of the film, in general, it is opaque light grey to dark grey, between the excessive so.
② Film thickness
Hard oxide film thickness is generally more than 50 microns, the greater the thickness of the oxide film, the more defects in appearance, the more cracks, the film thickness uniformity, continuity are worse.
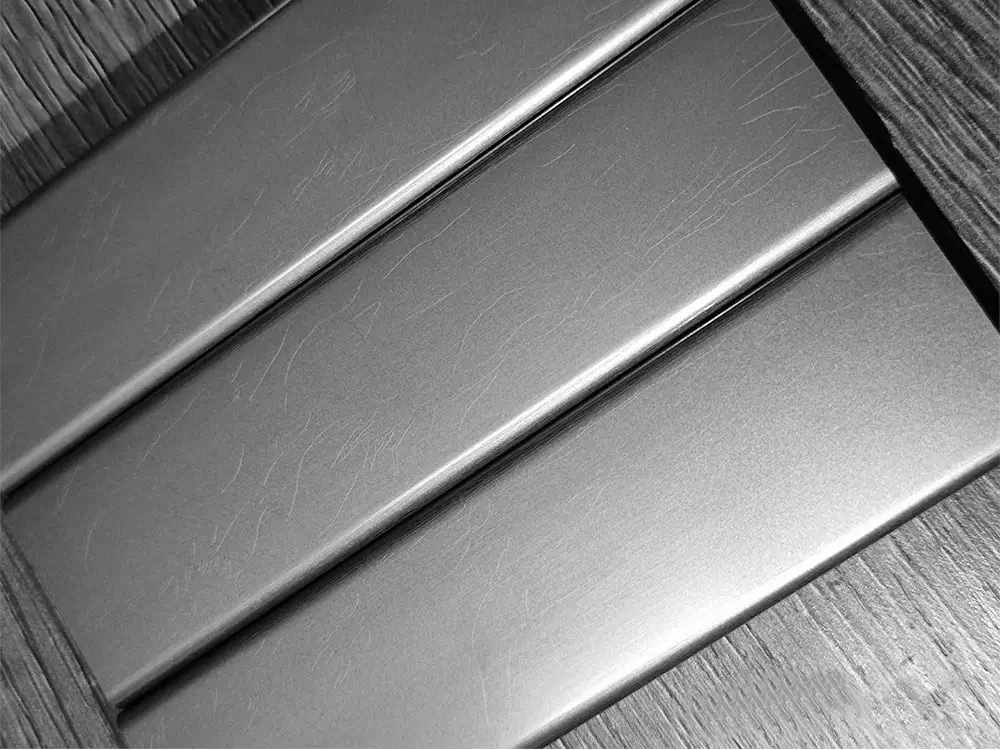
③ Hardness
hard oxide film hardness depends on the alloy composition and hard oxygen process, micro-hardness value even with the film cross-section and the relative position of the substrate, the closer to the substrate micro-hardness value is higher. The national standard on the Vickers microhardness qualifying value of the provisions of the 2-series alloys needs to be 250HV, other than the 2-series of deformed aluminum alloys, 400HV, high magnesium (Mg≥ 2%) 5-series and 7-series need to be 300HV.
④ Abrasion Resistance
Abrasion resistance is generally carried out in the unclosed oxide film, because at high temperatures, the abrasion resistance will be reduced by about 50%. Wear resistance of the oxide film of hard oxide is usually 1~2 times higher than that of plain oxide (except for Series 2 alloys).
⑤ Electrical insulation
Anodized films are all non-conductive, and the breakdown voltage of hard anodized films reaches even more than 1000V. If it is necessary to increase the breakdown voltage further, then the applied voltage at hard anodizing should be increased.
⑥ Corrosion resistance
The corrosion resistance of hard oxide film is generally stronger than that of conventional oxide film, but the hard oxide film is more prone to microcracks, so the ones after hard oxidation with nickel/non-nickel closure at room temperature tend to be more resistant to the salt spray test. At the same time, hard oxygen after increasing coating, paraffin, mineral oil, etc., can also be very good to improve the corrosion resistance of the film.
⑦ Heat resistance
Hard oxide film is a good heat dissipation “black body”, thermal emission with the increase in thickness of the oxide film increases rapidly, and the use of this feature can eliminate the heating parts of the hot spot, applied to some cookware materials.
⑧ Mechanical properties
Hard oxygen generally does not affect the mechanical properties of the material, but may lead to a reduction in the ductility and fatigue strength of the material, and the thicker the film layer, the greater the impact.
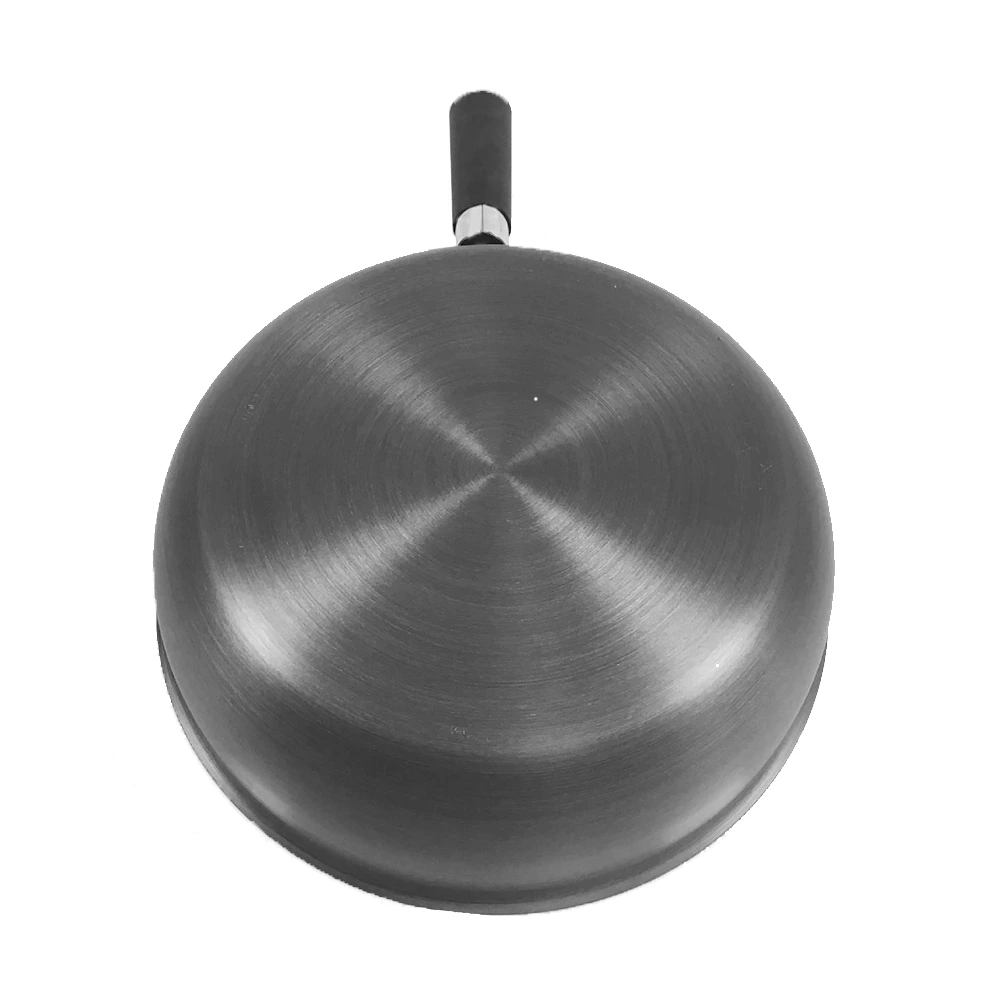
7. Aluminum Hard Anodizing Areas of Applications
Hard anodizing is widely used in areas with demanding requirements for surface properties:
Wear-resistant parts: hydraulic cylinder barrels, pistons, gears, guide rails, bearing housings, textile machinery parts, and pump body parts.
Insulation parts: electrical equipment base, insulating pads, and electronic components carrier.
Corrosion-resistant parts: marine environment parts, chemical equipment parts (often with closed or coated surfaces).
Aerospace: aircraft landing gear components, transmission system parts, and brackets.
Optical instruments: mirror barrels, precision instrument bases, laser parts (using their stability and insulation).
Workholding jigs and fixtures: Jigs and fixtures that require high abrasion and scratch resistance.
Cookware: some pots and pans, baking pans (utilizing their heat resistance, abrasion resistance, non-stick properties and heat emission properties, required to ensure food safety).
Decorative-functional combination: Decorative surfaces that provide high abrasion resistance, where a specific appearance (dark gray) is acceptable.
8. Quality Control and Precautions
Pre-treatment: Thorough degreasing, descaling and alkaline etching/acid pickling are essential to ensure a clean, revitalized surface, which is the basis for obtaining a uniform, high-quality film layer.
Precise temperature control: Temperature fluctuations are one of the most critical factors affecting the hardness and uniformity of the film layer.
Aluminum Ion Management: Aluminum ion concentration is regularly monitored and controlled in the optimum range.
Power Supply and Parameter Stability: Stable current/voltage output is critical to film layer consistency. Use appropriate power supplies and boosting procedures.
Workpiece clamping: Ensure good electrical conductivity and avoid contact point ablation. Design proper hangers and consider power line distribution.
Alloy selection: Select the appropriate aluminum alloy grade (give priority to Series 6, Series 5, Series 1) according to the final performance requirements (hardness, wear resistance, appearance) and processing difficulty.
Post-treatment and testing:
Thoroughly clean to remove residual acid.
Select the appropriate sealing process (room temperature sealing is preferred) or no sealing according to the needs.
Key testing items: film thickness (eddy current or metallography), hardness (microhardness tester), abrasion resistance, appearance, corrosion resistance test (e.g. salt spray test) and insulation test if necessary.
Microcracks: Recognizing that microcracks are an inherent feature of thick hard oxide films, it is necessary to optimize the process (e.g., adding organic acids, controlling parameters) to reduce their adverse effects and to compensate for their potential impact on corrosion resistance through post-treatments such as closure.
9. Highly Wear-Resistant and Insulating Hard Anodizing
YP-MFG relies on an advanced electrolytic deposition process and a precise temperature control system (±2℃) to strictly regulate the film thickness (50-100μm) and oxidizing time to ensure that each hard oxide part achieves >350HV hardness and long-lasting corrosion resistance.
Our professional team is deeply committed to the ISO 10074 hard oxidation process, providing:
- Customized solutions – optimized process parameters for 1/2/5/6/7 series aluminum alloys
- Zero burnout guarantee – pulsed power supply + step-up technology
- Full process Quality control – from surface pre-treatment to closure process tracking
Submit your part requirements today
YP-MFG’s engineers will customize a hard oxygen solution that extends your service life by 3-5 times!